Piezoelectric Low Frequency Energy Harvesters and their Use
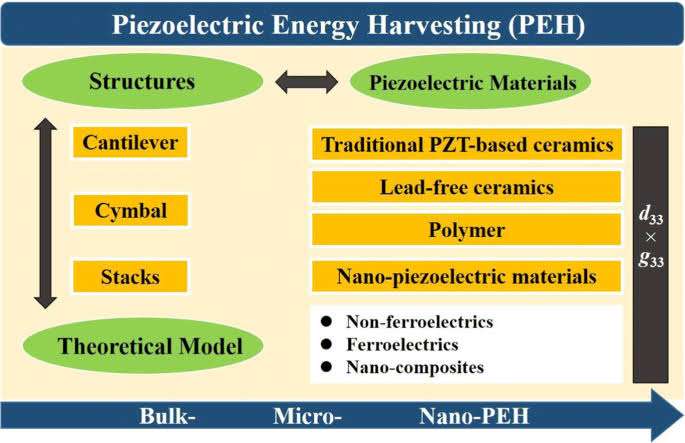
Several natural and industrial processes generate mechanical energy that goes wasted.
This energy can be harvested and converted to electric output energy through the piezoelectric effect.
Piezoelectric energy harvesters can function as both sensors and power generators.
In addition, they can be integrated into civil and engineering structures for structural health monitoring.
How does Piezoelectric Energy Harvester work to Produce Energy for machines?
Using piezoelectric energy harvesters is an environmentally friendly way to capture mechanical vibrations for power generation.
By converting kinetic energy into electrical energy, these devices can eliminate the need for batteries to power electronics.
These systems can also be used to self-power environmental sensors and wireless monitoring devices.
The kinetic energy found in fluid flow can also be harvested with piezoelectric energy harvesters.
These energy harvesters convert kinetic energy from the flow of water or air into electricity.
Typically, a piezoelectric energy harvester consists of a piezoelectric material and a power conditioning circuit.
When the piezoelectric material is subjected to mechanical vibrations, its crystal lattice deforms, generating an electric charge.
This electric charge can then be converted into a DC by the power conditioning circuit.
To increase the output of piezoelectric energy harvesters, researchers have experimented with different excitation methods and structures.
One such technique is frequency-tuning synchronized charge extraction (FTSECE), which reduces the voltage drop during energy harvesting.
Another method is to use a nonlinear oscillator as the source of excitation, which increases the power density of the harvester.
One issue with piezoelectric energy harvesters is that their natural frequencies are relatively high, making them less efficient for low-frequency applications.
To overcome this problem, some researchers have proposed introducing additional inertial mass into the system.
This can improve the energy efficiency of the harvester, but it may increase its size and weight. In addition, the added mass may lead to fatigue growth of the generator.
Researchers have also developed new materials for piezoelectric energy harvesters that can withstand higher pressures and loads.
A key component of these materials is a new type of piezoelectric material called polyvinylidene fluoride, or PVDF.
This material can withstand higher strain levels than PZT and has a much better tensile strength value.
Moreover, the PVDF can withstand high temperatures, which is necessary for the efficient operation of piezoelectric energy harvesters in harsh environments.
Lastly, the PVDF can be shaped into a variety of shapes to improve its performance in a wide range of applications.
How to Improve the Frequency Response and Performance of Piezo Energy Harvesters?
A piezoelectric energy harvester can be structured in various ways to increase its efficiency.
One way to achieve this is by widening its frequency bandwidth. This can be done either passively or actively.
In a passive approach, the natural resonant frequencies of the structure are altered by adding inertial mass.
The addition of inertial mass lowers the resonant frequencies of the system and improves its energy-harvesting performance.
However, inertial masses increase the size and weight of the system, limiting its applications.
Another way to broaden the frequency response of a piezoelectric energy harvester is by active modal control.
This method consists of actuating the energy harvester based on the displacement and acceleration feedback.
It can also be used to tune the resonant frequency of the energy harvester to match the excitation frequency. This can be accomplished with low power consumption.
Piezoelectric energy harvesters can be built on a range of substrates, including metal, polymer, and composite materials.
To maximize the efficiency of the energy harvester, it is important to choose a suitable material that matches the vibration frequency of the environment.
Metals have the highest electromechanical coupling coefficient, followed by polymers and then composites.
To improve the performance of a piezoelectric energy harvester, researchers have developed several structures that can be used to generate more output power.
The most common design is the cantilever beam configuration, which uses either one or two layers of piezoelectric materials.
These piezoelectric layers are bonded to a metallic non-piezoelectric layer. The two-layer configuration is referred to as bimorph, while the single-layer configuration is called unimorph.
Another way to improve the performance of a piezoelectric device is to use a frequency-tuning synchronized charge extraction (FTSECE) circuit.
This technique obviates the problems associated with SECE circuits such as narrow frequency bandwidth in strongly coupled generators and disability in providing maximum power by controlling voltage drop at the point of charge extraction.
Piezoelectric energy harvesters are ideal for powering wireless sensor networks that monitor environmental parameters, structural health, or industrial processes.
They provide a sustainable and renewable power source that eliminates the need for batteries, reducing the cost of maintenance.
In addition, they can be used to charge portable electronics such as smartphones or tablets.
They can also be incorporated into wearable devices such as smartwatches and fitness trackers.